Ouvrir la voie du succès numérique : Combinaison de l’industrie 4.0 et du lean management
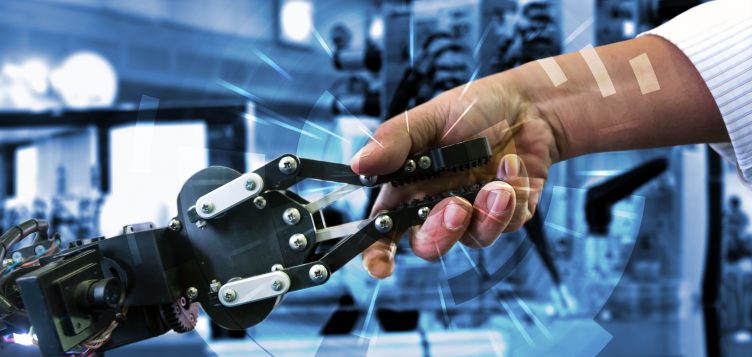
Quels sont les éléments clés de l’industrie 4.0, comment une numérisation lean peut-elle fournir un meilleur environnement économique pour tous ? Quels sont les écueils les plus fréquents pour les entreprises s’engageant dans des transformations numériques ? Nous discutons avec l’équipe de consultants et d’experts en lean management, Four Principles, afin d’approfondir ces questions.
Dans tous les secteurs, les entreprises qui réussissent s’efforcent continuellement d’augmenter la vitesse, l’efficacité et les profits en optimisant leurs opérations de plus en plus complexes.
Néanmoins pour garder une longueur d’avance dans l’environnement économique extrêmement concurrentiel actuel, les entreprises sont soumises à une pression continue pour réaliser des gains de productivité, améliorer la qualité et la prestation de services à la clientèle. Ces dernières années, le terme « industrie 4.0 » en est venu à désigner la prochaine vague d’opportunités pour les entreprises les plus ambitieuses, cherchant à exploiter les nouvelles technologies afin d’optimiser leurs performances.
Que signifie industrie 4.0 ?
Le concept d’industrie 4.0 représente le quatrième bouleversement significatif dans la production moderne, après l’introduction des systèmes de fabrication mécaniques vers la fin du 18e siècle, la production en série et l’énergie électrique au 20e siècle et l’automatisation soutenue par l’électronique dans les années 70.La plupart des tendances disruptives que recouvre l’industrie 4.0 sont liées aux progrès des technologies numériques. Selon McKinsey, elle est portée par « quatre bouleversements[1] » :
- L’augmentation de la puissance de calcul, des volumes de données et de la connectivité
- L’émergence des capacités analytiques et de veille économique
- Le développement de nouvelles façons d’interagir avec la technologie, notamment les écrans tactiles et la réalité augmentée
- L’introduction de la robotique, de l’impression 3D et d’autres moyens d’introduire des instructions numériques dans le monde physique
L’industrie 4.0 représente un changement radical dans la façon dont les entreprises envisagent et mettent en application la technologie dans chaque sphère de leurs opérations, et permet de réaliser des gains considérables en matière d’efficacité et de performance. Mais l’histoire ne s’arrête pas là. En combinant le potentiel technologique de l’industrie 4.0 aux principes du lean management axés sur la performance, les entreprises peuvent démultiplier les opportunités d’amélioration et bénéficier d’avantages concurrentiels considérables.
Le Boston Consulting Group (BCG) indique qu’une approche combinée est de loin la plus avantageuse : alors que des introductions séquentielles ou indépendantes de l’industrie 4.0 et des principes lean offrent certains avantages, « dans la plupart des cas, l’application intégrée du lean management et du concept d’industrie 4.0 – que nous appelons Lean Industry 4.0 – s’avère la manière la plus efficace d’atteindre le prochain niveau d’excellence opérationnelle[2] ».
Cette différence tient « au fait que l’approche intégrée permet au lean management et à l’industrie 4.0 de se stimuler mutuellement », c’est à dire que leur potentiel d’amélioration est plus grand que la somme des améliorations de l’une ou l’autre approche prise individuellement[3].
Comprendre les conséquences pratiques
Les principes lean préconisent « la création d’une culture forte orientée sur la maximisation de la valeur client tout en réduisant le gaspillage, avec pour objectif de maintenir l’alignement des efforts vers l’obtention de résultats commerciaux clairs par le biais d’une utilisation disciplinée de mesures[4] ».
Lorsque cette approche est associée aux puissants leviers numériques de l’industrie 4.0, qui vont de la gestion numérique des performances et la surveillance à distance, à la consommation intelligente d’énergie et à la maintenance prédictive, il existe un potentiel considérable pour créer de la valeur en améliorant la qualité, l’utilisation des actifs, les délais de commercialisation et la gestion des ressources et du personnel.
Rien que l’utilisation de l’analytique avancée, selon McKinsey, pourrait permettre à la plupart des entreprises d’améliorer leur marge brute de 30 % dans un délai d’à peine deux ans[5].
Les domaines clés dans lesquels les entreprises ont appliqué cette approche afin de réaliser des gains exponentiels incluent :
- Le Big Data (mégadonnées), qui permet aux organisations de dégager des rendements importants. Par exemple, une compagnie d’exploitation minière africaine a économisé 20 millions USD par an après avoir identifié un nouveau moyen de collecter plus de données depuis ses capteurs[6].
- L’analytique avancée, pour améliorer de façon drastique le développement de produits. Un fabricant automobile, par exemple, a associé des données en ligne et d’achat afin de réduire ses options pour un modèle à 13 000 (son concurrent en offrait 27 000 000).
- Les interfaces homme-machine, comme les casques à réalité augmentée utilisés par Knapp AG pour aider le personnel à trouver plus rapidement des articles, et réduire les taux d’erreur de 40 %, avec une caméra intégrée capturant les numéros de série pour un suivi de l’inventaire en temps réel[7]. L’Office de l’électricité et des eaux de Dubaï (DEWA) emploie également une technologie similaire pour aider à surveiller ses turbines[8].
- Les transferts numérique-vers-physique, exploités avec succès par Local Motor. La société construit désormais des voitures « presque entièrement par impression 3D » et a réduit le temps de développement d’un nouveau modèle de six ans à un an[9]. Sans surprise, des fabricants majeurs, tels que Vauxhall et GM, explorent déjà les avantages potentiels de l’impression 3D.
- Les capteurs sophistiqués – dans l’industrie papetière, des capteurs de température à distance surveillent les indicateurs clés, tandis que des outils dernier cri analysent et ajustent automatiquement l’intensité de la flamme du four. Les avancées technologiques ont permis jusqu’à 6 % d’économies de carburant et une augmentation du rendement de 16 %.
Les transformations numériques impliquent souvent une lutte incessante
Il est impossible d’ignorer les avantages potentiels de l’industrie 4.0. De fait, BCG a constaté que 97 % des responsables de production dans l’industrie automobile pensent que le lean management se révèlera hautement pertinent en 2030 (comparé à 70 % en 2017) et 70 % pensent que la numérisation des usines sera hautement pertinente en 2030 (comparé à 13 % en 2017).
Pourtant la décision de mettre en œuvre l’industrie 4.0 lean requiert toujours une planification rigoureuse. Plus de huit transformations numériques sur dix échouent et seulement 50 % des entreprises réussissent à mettre en place leurs stratégies de transformation numérique, en dépit des efforts et des investissements réalisés. En termes monétaires, le Genpact Research Institute estime que les grandes entreprises gaspillent une moyenne de 400 milliards USD par an dans des projets de transformation numérique qui, finalement, n’apportent pas les avantages promis[10] – et il n’est pas difficile de trouver des exemples notoires de transformations numériques ayant mal tourné :
- Le fabricant danois de jouets, LEGO, a annulé le financement de son programme exclusif de construction virtuelle, Digital Designer, et a cessé de fournir des mises à jour en 2016.[11] Sorti en 2004, le programme faisait partie d’une stratégie visant à améliorer les expériences des clients, sur la base d’instructions automatisées pour les modèles personnalisés.
- Le géant du secteur des articles de sport, NIKE, a réduit de moitié son département numérique en 2014, et a mis fin à ses tentatives de production de matériel portable. L’entreprise n’a pas réussi à créer une expérience de qualité supérieure que les clients seraient prêts à acheter dans un marché concurrentiel.[12]
- Le diffuseur britannique, BBC, a abandonné son projet d’innovation numérique de 100 millions GBP,[13] dont l’objectif était de transformer le développement, l’utilisation et le partage des documents audio et vidéo par le personnel. Son directeur général a admis que l’entreprise avait « gaspillé une énorme quantité de l’argent des contribuables ».
Comprendre correctement la transformation numérique
Pour tirer parti des avantages de l’industrie 4.0 et de la numérisation associée, les entreprises doivent changer la façon dont elles conduisent leurs affaires – il ne s’agit pas uniquement d’installer une nouvelle technologie.
« Lorsqu’une force transformationnelle telle que l’industrie 4.0 devient complètement évidente, il est déjà presque trop tard. Il est impératif pour les entreprises d’agir maintenant – attendre trop longtemps pourrait considérablement entraver la croissance et la rentabilité. »
James Ryan, consultant principal chez Four Principles
« L’industrie 4.0 requiert des changements fondamentaux en matière d’infrastructure, de conception de projets, de processus opérationnels et d’opérations individuelles, une entreprise extrêmement complexe si elle est correctement mise en place », déclare James Ryan, consultant principal chez Four Principles. « Tirer parti de l’industrie 4.0 exige également un engagement de la haute direction, des améliorations et un contrôle continus. »
Le lean management est conçu pour parvenir à l’excellence opérationnelle et est extrêmement approprié dans le contexte de l’industrie 4.0. « Les fabricants s’efforçant d’optimiser leurs opérations en adoptant des tendances de l’industrie 4.0 peuvent le faire bien plus efficacement en intégrant les principes du lean management », déclare Stefano Gaspari, consultant principal chez Four Principles. « Nous sommes convaincus que cette approche holistique en deux parties a de plus grandes retombées et permet de capter le maximum d’avantages. La stimulation mutuelle offre des avantages qui vont bien au-delà de l’industrie 4.0. »
Les principes éprouvés de la pensée lean sont fondamentaux dans la mise en œuvre efficace de l’industrie 4.0. Par exemple, une numérisation réussie exige une pensée transformationnelle à travers toute l’organisation, pas uniquement au sein du département informatique. En évaluant les chaînes de valeur dans leur intégralité, en supprimant le gaspillage, en lançant et en tirant les enseignements des projets pilotes phares, en soutenant une innovation continue par l’introduction de nouveaux comportements, la pensée lean envisage l’entreprise comme un tout.
Combinaison de l’automatisation et de l’intelligence humaine
Tandis que les entreprises veulent profiter des progrès de l’industrie 4.0 en automatisation, l’implantation du lean dans l’industrie – qui remonte à plusieurs décennies jusqu’au Toyota Group, et même avant avec Henry Ford, qui aurait mis en place le premier processus rudimentaire de production lean – s’avère particulièrement pertinente.
Dans le lexique lean, le « jidoka » représente la combinaison de l’automatisation et de l’intelligence humaine ou, en d’autres termes, l’automatisation avec une touche humaine.
Le concept de « jidoka » est un des piliers du système de production de Toyota et remonte au début du XXe, lorsque Sakichi Toyoda a inventé un mécanisme simple pouvant détecter un fil cassé et mettre à l’arrêt un métier à tisser automatique.
L’invention a permis qu’un seul opérateur puisse surveiller de nombreux métiers à tisser tout en maintenant des normes de haute qualité.
Avec le « jidoka » dans le monde moderne, une machine automatisée peut détecter un problème, le communiquer, et arrêter la chaîne de production.
Le responsable humain résout ensuite le problème, et des améliorations sont incorporées dans le flux de travail standard. Avec le modèle « jidoka », aucun produit défectueux n’est fabriqué, puisque la ligne d’assemblage se retrouve à l’arrêt – et un seul opérateur peut surveiller plusieurs machines, puisqu’elles sont conçues pour s’arrêter automatiquement, ce qui permet d’obtenir des améliorations drastiques de la productivité.
Dans le monde numérique, l’intégration de logiciels permet désormais aux entreprises d’analyser les masses de données en temps réel, y compris le statut de la production et la consommation d’énergie. Ces progrès en automatisation signifient que les ressources sont rapidement redistribuées, ce qui permet des économies de coût, et rend les systèmes de production plus flexibles.
L’entreprise de construction mécanique, Bosch Rexroth, construit une « usine du futur », où tout est connecté, du terrain jusqu’aux systèmes informatiques basés sur le Cloud. Les solutions logicielles sophistiquées collectent, transfèrent et traitent les données issues des processus de fabrication automatisés afin que les humains les analysent et les optimisent. L’entreprise place les humains au centre de ses efforts, qu’il s’agisse des utilisateurs, concepteurs et décideurs. Cet échange constant d’informations stimule la collaboration intelligente et la flexibilité. Au final, les coûts unitaires faibles et la production économique de lots, qui peuvent ne contenir qu’un seul article, bénéficient aux clients de Rexroth.
L’industrie 4.0 et le concept « jidoka » ne se limitent pas aux environnements de production. Le prestataire de santé régional à but non lucratif, Virginia Mason, basé à Seattle, a eu recours au concept de « jidoka » afin d’intégrer la technologie d’administration de médicaments via code-barres (Barcode Medication Administration, BCMA) dans son flux de travail infirmier avec des perturbations minimales. Avec la BCMA, une infirmière scanne le code-barres du bracelet d’un patient afin de vérifier l’identité du patient, puis scanne le code-barres sur le médicament afin de s’assurer que le médicament correct est administré, avec le dosage, la technique et l’horaire appropriés. Bien que le code-barres fournisse des informations précieuses, l’infirmière dispose du pouvoir décisionnel final.
La BCMA représente l’automatisaton numérique, tandis que le jugement humain intelligent de l’infirmière concrétise le concept de « jidoka ». Après la mise en œuvre de la BCMA, le nombre de violations des bonnes pratiques de dosage est passé de 54,8 à 29 par 100 doses, et le nombre d’erreurs d’administration de médicament a diminué également, passant de 5,9 à 3 par 100 doses.
Lorsqu’il est question d’adopter l’industrie 4.0, les principes éprouvés du lean, tels que le « jidoka », offrent des bases de réussite solides. McKinsey affirme que « l’industrie 4.0 sera moins une révolution qu’une évolution précieuse (et bienvenue), autorisant des gains de productivité de niveau supérieur et reflétant les développements survenus dans les processus de production pendant plus d’un siècle[14] ».
Si votre entreprise est prête à s’engager dans une aventure numérique transformationnelle, Four Principles est en mesure de fournir une expertise lean concrète, qui bénéficie de la confiance de chefs d’entreprise issus de pays aussi divers que le Maroc, l’Égypte, la Chine, l’Irlande, l’Espagne et la Suisse.
Pour plus d’informations, consultez fourprinciples.com.
[1] Manufacturing’s next act, McKinsey, June 2015
[2] When Lean Meets Industry 4.0, BCG, 14 December 2017
[3] When Lean Meets Industry 4.0, BCG, 14 December 2017
[4] A Lean Digital Future for More Tangible Impact – Putting Digital Transformation To Work (& II), Jose de la Rubia, 5 December 2017
[5] Manufacturing’s next act, McKinsey, June 2015
[6] Manufacturing’s next act, McKinsey, June 2015
[7] Manufacturing’s next act, McKinsey, June 2015
[8] Mixed Reality for Industry 4.0, Forbes, 12 July 2018
[9] Manufacturing’s next act, McKinsey, June 2015
[10] Genpact Introduces Lean Digital(SM) – A Unique Approach That Delivers Digital’s Full Potential and Helps Reclaim Over $400 Billion of Impact, PR Newswire, 16 September 2015
[11] https://www.brothers-brick.com/2016/01/21/lego-digital-designer-officially-defunded-and-unsupported-news/
[12] https://www.cnet.com/news/nike-fires-fuelband-engineers-will-stop-making-wearable-hardware/
[13] https://www.theguardian.com/media/media-blog/2014/feb/03/bbc-digital-media-initiative-failed-mark-thompson
[14] Industry 4.0 demystified – lean’s next level, McKinsey, March 2017