デジタルの長所を最大限に活用: インダストリー4.0とリーン経営の統合
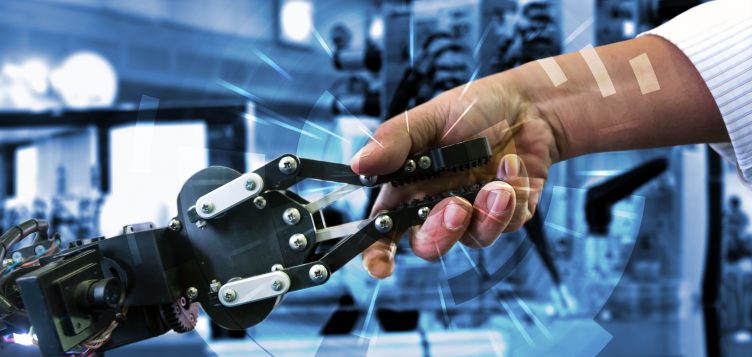
インダストリー4.0の主軸は何でしょうか?どうすれば、リーンデジタリゼーションによって、万人により望ましいビジネス環境を確率できるでしょうか?デジタル変革に乗り出している企業にとって、よくある落とし穴とはどのようなものでしょうか?リーン経営のエキスパートである
Four Principles社のコンサルタントチームと話をして、詳しく探ります。
業界を問わず、成功している企業は、ますます複雑化する業務を最適化することによって、スピード、効率、利益の向上を常に目指しています。
しかし、現在の競争熾烈なビジネス環境で先頭を走るために、企業は、生産性、品質、そしておそらく最も重要なことであるカスタマーサービスの提供においても、何か得るものがなくてはならないという絶え間ないプレッシャーにさらされています。近年では、「インダストリー4.0」という言葉が、極めて意欲的な企業が新技術を活用して業績最適化を目指す次の機会の波を表すようになってきました。
インダストリー4.0とは?
「インダストリー4.0」とは、18世紀後半の機械製造導入、20世紀の大量生産と電気エネルギーの導入、1970年代のエレクトロニクス主導型オートメーションに続く、現代製造業における4度目の大変革のことです。 インダストリー4.0に含まれる革命的トレンドの大部分は、デジタル技術の進歩に関わるものです。McKinseyによると、このトレンドを主導しているのは次の「4つの革命[1]」です。
- 演算能力、データ量、接続性の向上
- 分析能力とビジネスインテリジェンス能力の出現
- タッチスクリーンや拡張現実など、これまでなかった技術との対話的な手法の開発
- ロボティクス、3Dプリント、デジタルインストラクションを現実世界に普及させるその他の方法の導入
インダストリー4.0は、業務のあらゆる面で企業の物の見方や技術実装方法を段階的に変えていくことです。効率性と能力に顕著な利益をもたらす可能性があります。しかし、話はそれで終わりではありません。インダストリー4.0において技術が主導する潜在的可能性と、パフォーマンスを重視するリーン管理の原理を組み合わせることによって、企業は、大きな進歩と著しい競争上の優位性を切り開けるようになるでしょう。
The Boston Consulting Group(BCG)は、統合型アプローチには非常に大きなメリットがあり、さらにインダストリー4.0とリーンの原理を個別に、または連続して導入することには、いくつかのメリットがあると紹介しています。「多くの場合、我々が『リーン・インダストリー4.0』と呼ぶリーン経営とインダストリー4.0の統合的利用は、オペレーショナルエクセレンスの次のレベルに到達するための最も効果的な方法です[2]。」
違いは「統合して利用すれば、リーン経営とインダストリー4.0が相互に力を発揮できるから」。つまり、統合型のほうが、どちらか一方のアプローチが個別に実現する改善の総和よりも改善の可能性が大きいというわけです[3]。
実際的影響を理解する
「顧客価値の最大化に注力する強力な文化を醸成する一方で、無駄を最小限に抑え、評価指数をしっかり使用することによって明確な事業成果に向けて取り組みを調整し続けることを目指す[4]」というのが、リーン原理の主張です。
このアプローチを、デジタル性能管理やリモート監視からスマートなエネルギー消費、予知保全まで多岐にわたるインダストリー4.0という巨大なデジタルの力を組み合わせた場合、そこには、品質、資産活用、市場化にかかる時間、リソースや労働力の管理を改善することによって価値を創出する大きな潜在的可能性があります。
McKinseyによると、先進分析のみを使うことで、大半の企業はほんの2年以内に粗利益を30%増やせます[5]。
以下は、指数的な利益を達成するために企業がこのアプローチを応用した主な領域の例です。
- ビッグデータ。ビッグデータを用いることで、組織は顕著な結果を出せます。例えばアフリカの鉱業会社は、センサーで捉えるデータを増やす新しい方法を見つけた後、年間2,000万米ドルを節約しました[6]。
- 先進分析。製品開発を劇的に改善するために利用できます。例えば、ある自動車会社はオンラインデータと購入データを組み合わせて、1モデルのオプション数を13,000にまで減らしました(競合他社の提示数は27,000,000でした)。
- ヒューマン・マシン・インターフェース。Knapp AGで用いられる拡張現実ヘッドセットなどは、スタッフがアイテムを速やかに見つけて、エラー率を40%減らすのに役立ちます。リアルタイム在庫追跡用に、組み込まれたカメラを使ってシリアル番号を記録します[7]。Dubai Electricity and Water Authority(DEWA)も、タービンのモニタリングに役立てるために類似技術を使用しています[8]。
- デジタルからフィジカルへの移行。Local Motors社が“ほぼ完璧な3Dプリント”自動車製造にこれを利用して成功しました。新モデル開発時間を6年から1年に短縮しています[9]。当然、VauxhallやGMといった大手メーカーはすでに、3Dプリントの潜在的メリットを調査中です。
- 高性能センサー – 紙パルプ業界では、遠隔温度センサーが主要なインジケーターを監視すると同時に、最新ツールが窯の火の強度を分析し、自動調整します。この技術的進歩の結果、最大6%の燃料節約となり、スループットは16%向上しました。
苦戦になりがちなデジタル変革
インダストリー4.0の潜在的メリットを無視することはできません。確かに、BCGの所見によると、自動車業界では(2017年の70%と比較して)97%の生産マネージャーが、2030年までにリーン経営が大きな影響力をもつようになると確信し、(2017年の13%と比較して)70%の生産マネージャーが2030年までに工場のデジタル化が大きな影響力をもつようになると確信しています。
それでも、リーン・インダストリー4.0を実践するかどうか決定するには、本気で計画を立てなければなりません。努力や投資を行っていることは明らかなのにもかかわらず、10件のデジタル変革のうち失敗件数は8件を超えます。デジタル変革戦略を首尾良く実施しているのはわずか50%の企業です。財務面では、大規模エンタープライズがデジタル変革プロジェクトで年間平均4,000億米ドルを無駄にして、約束した利益を出せていないと、Genpact Research Instituteが算出しています[10]。デジタル変革の明らかな失敗例を探すことは難しくありません。
- デンマークの玩具メーカーLEGO社は、2016年に自社開発「Digital Designer」仮想組み立てプログラムへの出資を打ち切り、更新を中止しました。[11]2004年に発表された同プログラムは、オーダーメイドモデル向け手引きの自動化をベースにカスタマー・エクスペリエンスを向上させる戦略の一環でした。
- 巨大スポーツウェア企業NIKEは、2014年にデジタルユニットを半分に縮小し、ウェアラブルハードウェア事業から撤退しました。同社は、競合分野で消費者が代価を払いたいと思うプレミアムな体験の創出に苦心したためです。[12]
- 英国の放送局BBCは、スタッフの開発、利用、動画と音声素材の共有方法を変革することを目的とした1億ポンドのデジタル・イノベーション・プロジェクトを諦めました[13]。「視聴者の受信料を膨大に無駄にした」と同社社長が認めています。
デジタル変革を正しく理解する
インダストリー4.0と関連するデジタル化のメリットをうまく捉えるには、企業は、業務遂行方法を変革しなければなりません。新しい技術を詳しく調べるという問題だけではないのです。
「インダストリー4.0などの変革の影響力が完全に明らかになる頃には、ほぼ遅すぎます。企業は、今すぐ行動すべきです。後回しにしすぎるのは、成長と収益の大きな妨げになります。」
Four Principles社プリンシパルコンサルタント、ジェームズ・ライアン氏
「インダストリー4.0では、インフラ、プロジェクト設計、ビジネスプロセス、人材運用の抜本的改革が必要です。適切に行うと、非常に複雑な試みになります。」と、Four Principles社プリンシパルコンサルタント、ジェームズ・ライアン(James Ryan)氏は述べます。「インダストリー4.0からメリットを得るには、トップリーダーシップのコミットメント、継続的なモニタリングと改善も欠かせません。」
リーン経営は、オペレーショナルエクセレンスの実現を目的としたもので、インダストリー4.0の前後関係に大きな影響力をもっています。Four Principles社プリンシパルコンサルタントのステファノ・ガスパリ(Stefano Gaspari)氏のコメントです。「インダストリー4.0というトレンドを応用することによって業務を最適化しようとしているメーカーは、リーン経営の原理を統合することによって効率を極めることができます。この2部から成る全体論的アプローチが極めて大きな影響力を生み出し、最大の利益を獲得すると、私たちは確信しています。相互実施可能性が、インダストリー4.0のみにとどまらないメリットを推し進めるのです。」
定評あるリーン思考の原理は、インダストリー4.0を効果的に実施する際の基盤です。例えば、デジタル化成功には、IT部門だけでなく、組織全体にわたる変革思考が求められます。バリューチェーン全体、無駄の排除、旗艦パイロットプロジェクトを評価し、新しい行動の創出を通して継続的なイノベーションを支援することにより、リーンは、企業を全体として考えます。
オートメーションとヒューマンインテリジェンスの統合
企業は、オートメーションにおけるインダストリー4.0の発展からめぼしいメリットを捉える立場にあるため、リーンの深い工業史は特に関連性があります。数十年さかのぼるとトヨタグループ、それよりさらにさかのぼるとHenry Fordには、基本的なリーン製造工程を開発した功績がありました。
リーン語の「自動化」は、オートメーションとヒューマンインテリジェンスの融合を表します。言い換えると、「人間味のある自動化」となります。
「自動化」は、糸切れを検出して自動織機を停止させることができる簡単なメカニズムを豊田佐吉が発明した1900年代初期に端を発する、トヨタ生産システムの主軸です。
この発明によって、作業員がたくさんの織機を監督しながら、高品質水準を維持できるようになりました。
現代世界で「自動化」を用いると、自動化された機械は問題を検出し、報告し、生産ラインを止めることができます。
その後、人間のマネージャーが問題を修正し、改善が標準ワークフローに反映されます。この自動化モデルのもとで、瑕疵のない製品が製造されます。ラインを停止し、1人のオペレーターが複数の機械を監視できるためです。機械は自動的に停止するよう設計されているので、結果として生産性が劇的に改善します。
デジタル界では、ソフトウェアの統合によって、今では企業が生産状況やエネルギー消費量などの大量のデータをリアルタイム分析できるようになりました。このように自動化が進歩すると、リソースが速やかに再分配されることになり、それによってコストが節約され、生産システムの柔軟性が向上します。
例えば、機械エンジニアリング会社Bosch Rexrothが構築している「フューチャーファクトリー」では、現場レベルからクラウドベースITシステムまで、すべてがつながっています。高度先進ソフトウェアが、人間が分析して最大化するために、自動化された製造プロセスからデータを収集し、転送し、処理します。会社は、人間を、ユーザー、設計者、意思決定者として、この取り組みの中心に位置付けています。この絶え間ない情報交換が、インテリジェントなコラボレーションと柔軟性を促進しているのです。究極的には、これがRexrothの顧客のメリットになり、単価は下がり、1アイテムほどの少ないロットサイズの経済的生産ができます。
インダストリー4.0と自動化は、製造環境にとどまりません。シアトルを拠点とする非営利地域医療提供業者Virginia Masonは、混乱を最小限に抑えながらバーコード投薬剤管理(Barcode Medication Administration、BCMA)技術を看護ワークフローに統合するために、自動化を採用しました。BCMAを用いて、看護師は患者のリストバンドに記載されているバーコードをスキャンして患者の個人情報を確認し、次に、医薬品のバーコードをスキャンして、正しい医薬品が適切な量、技術、タイミングで施されるようにします。バーコードが貴重な情報を提供する一方で、看護師は最終的な意思決定力をもち続けます。
BCMAはデジタル自動化です。その一方で、自動化の概念を完成させるのは、看護師のヒューマンインテリジェントな判断です。BCMA導入後、安全な投薬の違反数が投薬100回当たり54.8回から29回に減少しました。また、投薬ミス数は100回当たり5.9回から3回に減っています。
インダストリー4.0の採用に関して言うと、自動化などの長年の実績があるリーンの原理は、重要な成功基盤になります。「1世紀以上にわたってまったく新しい生産性の向上を実現し、製造環境で展開された開発を反映するなら、インダストリー4.0は、貴重な(そして願ってもない)発展というほどの革命ではなくなる[14]」と、McKinseyは主張しています。
貴社がデジタル変革の道のりに乗り出す準備をしている場合は、はるか遠くモロッコ、エジプト、中国、アイルランド、スペイン、スイスのビジネスリーダーが信頼を寄せている具体的なリーン経営のノウハウを、Four Principlesがご提供します。
詳しくはfourprinciples.comをご覧ください。
[1] Manufacturing’s next act, McKinsey, June 2015
[2] When Lean Meets Industry 4.0, BCG, 14 December 2017
[3] When Lean Meets Industry 4.0, BCG, 14 December 2017
[4] A Lean Digital Future for More Tangible Impact – Putting Digital Transformation To Work (& II), Jose de la Rubia, 5 December 2017
[5] Manufacturing’s next act, McKinsey, June 2015
[6] Manufacturing’s next act, McKinsey, June 2015
[7] Manufacturing’s next act, McKinsey, June 2015
[8] Mixed Reality for Industry 4.0, Forbes, 12 July 2018
[9] Manufacturing’s next act, McKinsey, June 2015
[10] Genpact Introduces Lean Digital(SM) – A Unique Approach That Delivers Digital’s Full Potential and Helps Reclaim Over $400 Billion of Impact, PR Newswire, 16 September 2015
[11] https://www.brothers-brick.com/2016/01/21/lego-digital-designer-officially-defunded-and-unsupported-news/
[12] https://www.cnet.com/news/nike-fires-fuelband-engineers-will-stop-making-wearable-hardware/
[13] https://www.theguardian.com/media/media-blog/2014/feb/03/bbc-digital-media-initiative-failed-mark-thompson
[14] Industry 4.0 demystified – lean’s next level, McKinsey, March 2017