Une philosophie pour une meilleure activité… et une vie meilleure
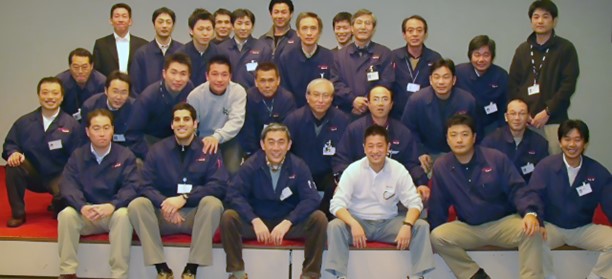
L’équipe Kaizen de Toyota Motor Corporation 2004 (Hassan Jameel est au premier rang, deuxième à partir de la gauche)
Une discussion avec Hassan Jameel sur Kaizen, et la manière dont une petite amélioration continue peut s’additionner à tant d’autres.
Quand Abdul Latif Jameel s’est associé pour la première fois à Toyota il y a près de 70 ans, il a importé bien plus que des voitures. Il a aussi importé une toute nouvelle approche de la gestion d’une entreprise.
Connue sous le nom d « amélioration continue », cette approche est basée sur la philosophie commerciale du « kaizen » mise au point par des sociétés japonaises comme Toyota pour accroître l’efficacité et les performances, éliminer le gaspillage et optimiser l’utilisation des ressources.
Henry Ford est reconnu comme avoir créer le premier processus de fabrication lean rudimentaire, lorsqu’il a introduit une chaîne d’assemblage mobile dans ses usines en 1913. Néanmoins, ce fut le travail de Kiichiro Toyoda, Taiichi Ohno ainsi que d’autres à Toyota au cours des années 1930 qui a perfectionné et développé l’idée originale de Ford afin de créer un véritable système de fabrication et de lean management.
En s’appuyant sur les méthodes de Ford comme source d’inspiration, ils ont établi le système de production de Toyota, et initié une révolution qui, au cours des décennies suivantes, a transformé les entreprises non seulement au Japon et aux États-Unis, mais aussi dans d’autres pays.
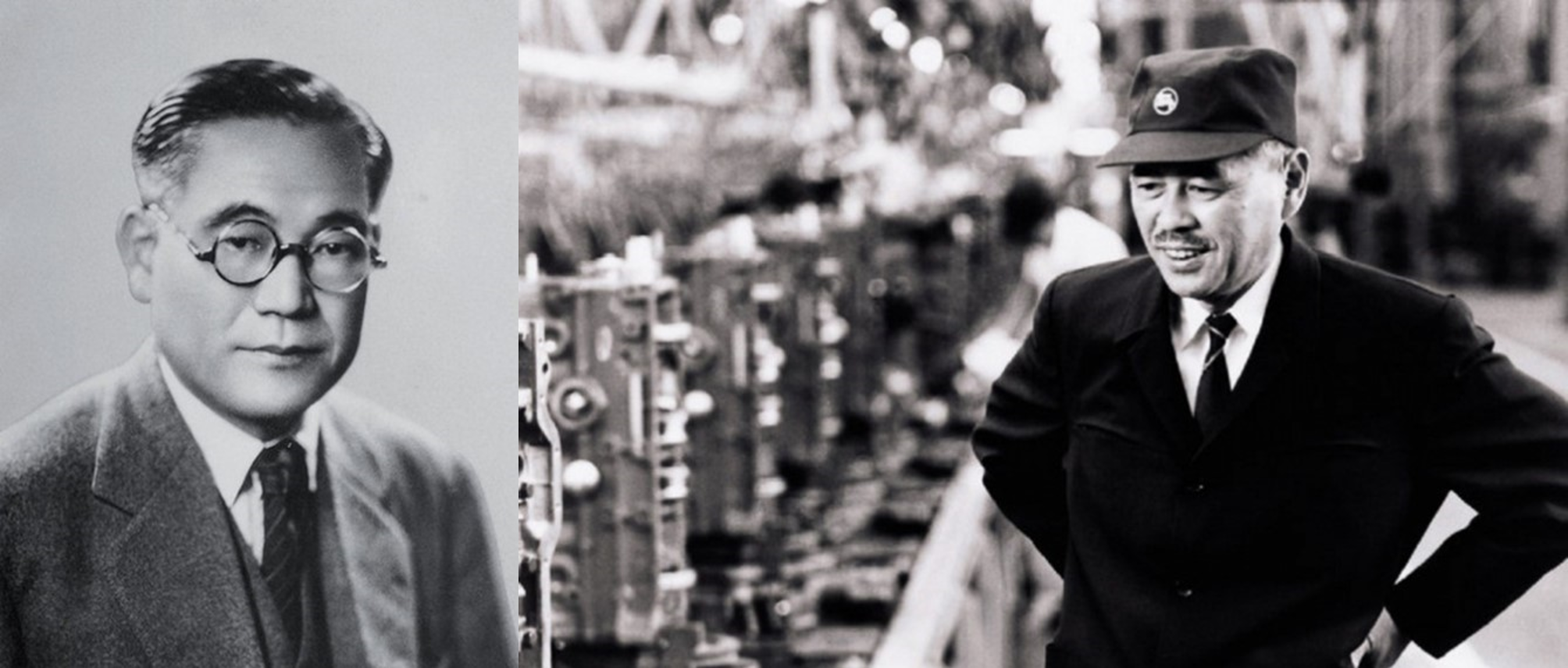
Kaizen, à savoir la façon dont les Japonais désignent ce processus d’amélioration continue, trouve son origine dans les processus de fabrication. Néanmoins, il peut être également appliqué aux entreprises de services. Les entreprises adoptant le lean management évaluent chaque action et chaque activité en recherche d’améliorations potentielles, indépendamment de leur importance. Ces gains peuvent s’avérer mineurs lorsqu’ils sont envisagés de façon isolée, mais considérés ensemble, ils ajoutent des améliorations considérables soutenant des changements positifs.
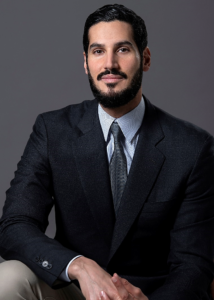
président délégué et vice-président
Arabie saoudite Abdul Latif Jameel.
Hassan Jameel, vice-président d’Abdul Latif Jameel Arabie Saoudite, est un fervent défenseur de la philosophie Kaizen. Il en a lui-même fait l’expérience lorsqu’il travaillait avec Toyota, à son siège social au Japon au début des années 2000.
Nous avons rencontré Hassan pour discuter de son intérêt pour l’amélioration continue et de la manière dont elle permet aux organisations de transformer la façon dont elles mènent leurs activités.
Qu’est-ce que « l’amélioration continue » ?
Et qu’est-ce que cela signifie pour vous ?
Contrairement à tout le jargon commercial et la terminologie de conseil, la définition de l’amélioration continue est extrêmement simple.
Tout est là, littéralement, au sein de ces deux mots. Toujours en amélioration. Essayer d’être meilleur en permanence. En surface, cela semble si évident. Mais c’est plus profondément ancré qu’il n’y paraît L’amélioration continue, pour moi en tant qu’individu, ne consiste pas seulement à s’améliorer chaque jour. Il s’agit de la façon dont vous incarnez cette mentalité dans votre mode de vie, jusqu’à devenir un automatisme.
Chaque jour, réfléchissez à ce que vous pourriez faire pour vous améliorer. Allez-y petit à petit : ce qui compte, c’est d’essayer d’améliorer quelque chose chaque jour. Ensuite, cela fera vraiment partie de votre identité.
Et c’est pareil dans les organisations. Comment créer une culture capable systématiquement de mettre en œuvre une approche d’amélioration continue dans tout ce qu’elles font, chaque jour, même s’il s’agit du plus petit changement ?
Une culture qui implique que tous les membres de l’entreprise réfléchissent continuellement à leur rôle, au rôle de leur équipe et aux tâches qu’ils effectuent dans le cadre de leurs fonctions, et aux petits changements qui pourraient être apportés au service d’une plus grande efficacité et une meilleure qualité. Chaque changement individuel peut, sur le moment, sembler sans conséquence. Mais tous les changements vont s’additionner. Petit à petit, même les plus petites étapes, lorsqu’elles sont rassemblées, font une grande différence. Je pense que c’est la simplicité qui rend l’amélioration continue plus efficace et plus facile à comprendre.
Quand avez-vous pris connaissance du concept d’amélioration continue pour la première fois ?
Je l’ai découvert quand j’étais très jeune, avant même de commencer à travailler dans l’entreprise. J’entendais mon père et d’autres cadres supérieurs en parler, et je savais que c’était quelque chose que l’entreprise faisait, mais je ne comprenais pas ce que cela signifiait.
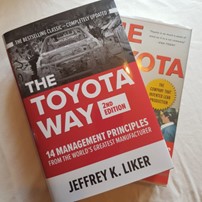
L’amélioration continue est basée sur la philosophie commerciale « Kaizen » lancée par Toyota.
Abdul Latif Jameel l’a découvert pour la première fois lorsqu’il a commencé à importer des véhicules Toyota en Arabie saoudite dans les années 1950. Mais en tant que philosophie d’entreprise, l’amélioration continue a vraiment atteint une importance mondiale dans les années 1990 et 2000. En 2001, Toyota, entreprise longtemps considérée comme l’un des pionniers du concept, a formalisé son approche du Kaizen avec la publication du « Toyota Way ».
Ce livre extrêmement influent est devenu le modèle permettant aux entreprises du monde entier de mieux comprendre l’amélioration continue et les avantages qu’elle pourrait apporter.
Ce n’est pas nécessairement japonais, au fait. Si vous vous rendez dans d’autres grandes entreprises japonaises, vous n’entendez pas nécessairement parler autant de Kaizen que lorsque vous allez à Toyota. C’est vraiment Toyota qui a pris ces idées et les a transformées en une philosophie d’amélioration commerciale, cohérente et pratique, autour du concept d’amélioration continue.
Plus tôt dans votre carrière, vous avez passé du temps au Japon, à étudier et à travailler chez Toyota. Comment cela a-t-il influencé votre compréhension de l’amélioration continue ?
J’ai suivi mes études secondaires et universitaires au Japon, et je passais souvent mes vacances à travailler en tant que stagiaire chez Toyota, en aidant sur de petits projets ici et là. Ce n’est qu’en 2004, quand j’ai rejoint la division nationale Kaizen de Toyota, que j’ai vraiment commencé à comprendre ce qu’impliquait l’amélioration continue au niveau pratique. J’étais la première personne non japonaise à intégrer cette division.
Le rôle de la division Kaizen était de travailler avec des concessionnaires au Japon et de les soutenir dans la mise en œuvre de projets Kaizen, dont la plupart étaient des projets opérationnels : chaîne d’approvisionnement, liés au service, gestion des stocks, etc. Nous avons travaillé avec eux pendant plusieurs mois pour créer et mettre en œuvre un processus d’amélioration continue et, plus important encore, nous avons assuré sa durabilité après notre départ.
Qu’est-ce que cela impliquait et qu’est-ce que cela vous a appris sur l’amélioration continue ?
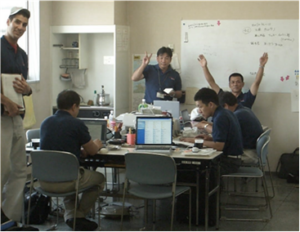
Hassan Jameel avec son équipe Kaizen Dept. 2004 au siège de Toyota Motor Corporation, Tokyo.
C’était un choc pour le système !
J’avais passé du temps dans différents environnements de travail, en dehors du Japon, où le mot « Kaizen » était utilisé comme raccourci assez vague pour améliorer une tâche.
Certains processus n’étaient pas aussi efficaces qu’ils auraient pu l’être, et quelqu’un disait « vous avez juste besoin de Kaizen ! », sans vraiment comprendre ce que cela signifiait exactement.
Lorsque j’ai été immergé dans l’équipe Kaizen au Japon, j’ai cependant réalisé qu’il y avait une philosophie très précise et structurée derrière le concept.
L’approche Kaizen repose sur un ensemble complet de principes qui touchent pratiquement tous les aspects de la culture et des méthodes de travail d’une entreprise. Cependant, au niveau du processus, c’est-à-dire lorsque vous souhaitez améliorer un processus spécifique, tout commence par les données. C’était la première mission que nous devions accomplir.
Nous nous tenions devant un ouvrier, cela pouvait être quelqu’un sur la ligne de nettoyage de la voiture, ou dans le centre de service d’entretien des véhicules, par exemple. Armés d’un chronomètre et d’un bloc-notes, nous notions tout ce qu’il faisait, ainsi que le temps qu’il y passait, pendant sa journée de travail. S’il allait aux toilettes, nous prenions note, s’il devait traverser le garage pour récupérer un outil, nous le notions, s’il devait aller chercher quelqu’un pour poser une question, nous le notions.
Nous le faisions pour toutes les personnes impliquées dans cette tâche, il nous fallait donc peut-être une semaine ou plus pour collecter toutes les données, que nous saisissions ensuite dans une feuille de calcul géante. Il y en avait une pour chaque ouvrier. Nous les affichions, nous les passions en revue ligne par ligne et y ajoutions des notes, en utilisant des couleurs différentes pour indiquer s’il s’agissait de temps perdu, de temps de travail ou de temps de travail improductif.
Je n’étais qu’un stagiaire à ce stade, et je ne comprenais pas tout ce que nous faisions. J’ai demandé à mon supérieur quel était le lien avec Kaizen. Comment cela pouvait nous rendre plus efficaces.
Il m’a répondu : « As-tu noté du temps perdu ? » Je lui ai dit qu’une personne avait dû quitter son poste de travail deux ou trois fois pour récupérer des outils. Il m’a demandé : « Combien de temps cela lui a-t-il pris ? » et j’ai répondu, selon les données, que cela lui avait pris six minutes au total. Il m’a demandé : « Comment pourrais-tu réduire ce temps ? » J’ai suggéré que si l’ouvrier avait eu les outils à côté de lui à son poste de travail, il n’aurait pas eu besoin de traverser la pièce pour aller les chercher, ce qui lui aurait fait gagner six minutes. Cette différence de six minutes me semblait insignifiante ! Mais il était ravi. Il m’a expliqué que si nous pouvions faire économiser six minutes à un technicien sur une journée, cela représentait une demi-heure par semaine. Si huit techniciens effectuent cette tâche, cela représente une économie de quatre heures par semaine, soit plus d’une demi-journée. Multipliez cela sur l’année, et c’est une économie massive. Combien de voitures supplémentaires pourraient être entretenues pendant ce temps ?
C’est à ce moment-là que j’ai vraiment commencé à comprendre en quoi consistait l’amélioration continue. Il ne s’agit pas de grandes idées coûteuses de la direction pour transformer le lieu de travail. Il s’agit de petites étapes qui s’ajoutent au fil du temps, pour instaurer une différence réelle et significative qui peut être maintenue.
Lors d’une autre mission, nous avons repeint l’entrepôt de stockage pour un concessionnaire. Nous l’avons fait nous-mêmes. Cela nous a pris environ 10 jours. C’était un travail difficile ! Nous étions dehors avec le vent, la neige et la pluie. J’ai demandé à mon supérieur pourquoi nous ne payions pas simplement quelqu’un pour venir peindre l’entrepôt. Il m’a expliqué qu’en le faisant par nous-mêmes, nous comprendrions le processus nous-mêmes et nous comprendrions comment l’améliorer. Ce qui nous permettrait de le faire mieux l’année suivante. En payant quelqu’un d’autre pour le faire, nous n’aurions pas pu acquérir ces connaissances.
La conviction qu’il ne s’agit pas de grandes idées, mais de petits changements, est très puissante, n’est-ce pas ? Parfois, dans les activités, il est plus facile d’investir de l’argent dans un problème que d’en analyser les véritables causes profondes.
C’est tout à fait vrai.
Mon supérieur m’a dit, un jour, que si vous vouliez résoudre un problème, il ne fallait pas l’alimenter… mais l’affamer.
Ce qu’il voulait dire, c’est que si vous identifiez un problème, n’en rajoutez pas. Pas de nouveaux processus, d’investissement ou de technologie supplémentaire. Identifiez plutôt le gaspillage, ou « muda » (en japonais), et multipliez-le par zéro. Autrement dit, éradiquez-le. Une fois que vous avez éliminé tout le gaspillage et le temps inutile, vous êtes revenu au processus le plus épuré : le « chemin critique ».
Cela vous donne la base à partir de laquelle vous pouvez commencer à retenter une amélioration progressive.
Il est facile de voir comment l’amélioration continue s’applique à une grande entreprise de fabrication. Peut-elle également s’appliquer aux petites entreprises ou aux prestataires de services ?
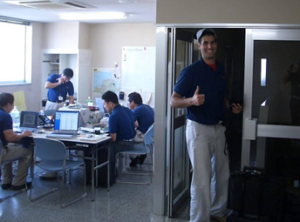
Elle peut s’appliquer à tout ce que nous faisons dans notre vie.
Deux des méthodologies expliquées dans le Toyota Way sont le Genchi Genbutsu et le Gemba. Elles visent toutes les deux à voir par vous-même le déroulé des processus sur le lieu de travail, à rendre visite aux ouvriers de la première ligne, à vous asseoir avec les gens, à les écouter, à comprendre comment ils fonctionnent et, plus important encore, pourquoi, afin de faire face aux problèmes par vous-même.
Cela peut s’appliquer à un environnement de bureau autant qu’à un atelier ou une ligne de production.
Lorsque j’étais à Toyota, nous travaillions au bureau un jour par semaine. Et nous voyions notre supérieur se déplacer dans le bureau, s’asseoir avec l’équipe de comptabilité ou parler aux ouvriers, poser des questions et prendre des notes. C’était le Genchi Genbutsu en action : il passait du temps avec les personnes en première ligne afin de comprendre leurs processus et les problèmes auxquels elles étaient confrontées.
Le respect joue un rôle important. Respecter nos collaborateurs, nos revendeurs, nos clients. Le respect ne consiste pas seulement à être gentil, à dire bonjour et bonne soirée à quelqu’un.
Il s’agit également de mettre en œuvre des politiques, des procédures et des normes qui créent un environnement respectueux pour les personnes. Où elles se sentent valorisées, où elles se sentent responsables de leurs propres performances, où elles se sentent écoutées et libres d’exprimer leurs opinions et de partager leurs idées.
Bien sûr, un élément clé de l’amélioration continue consiste à éliminer le gaspillage, y compris de temps. Et toutes les entreprises de tous les secteurs ont déjà perdu du temps, qu’il s’agisse de réunions inutiles, de rapports fastidieux, de bureaucratie écrasante. Ce sont tous des exemples de domaines dans lesquels une approche Kaizen peut améliorer l’efficacité et la productivité.
Comment Abdul Latif Jameel a essayé d’appliquer une approche d’amélioration continue sur le lieu de travail et quelle différence cela a-t-il fait ?
Chez Abdul Latif Jameel, nous avons un programme complet dédié au Kaizen appelé « le meilleur de la ville ». Il s’agit d’une initiative lancée par Toyota. On l’appelle « le meilleur de la ville » pour une raison. L’idée est que pour être les meilleurs de votre ville, vous devez parfaitement connaître votre marché local, vous devez comprendre pleinement les besoins de vos clients, et vous devez constamment répondre à ces besoins d’une manière beaucoup plus proche et plus significative que si vous visiez à être « le meilleur du monde », ce qui est un objectif beaucoup plus abstrait, par exemple.
Nous avons donc créé cette équipe du « meilleur de la ville » pour être les champions de l’amélioration continue au sein d’Abdul Latif Jameel ; pour aider toutes nos différentes entreprises et tous nos sites à comprendre la philosophie de l’amélioration continue et à savoir comment l’intégrer dans leurs propres activités. Nous venons d’organiser l’édition 2023 de la conférence régionale du « meilleur de la ville » en Arabie saoudite, avec plus de 150 représentants d’équipes à travers le monde pour partager leurs idées, leurs expériences et leurs réussites basées sur une amélioration continue dans une grande variété d’entreprises et de secteurs industriels.
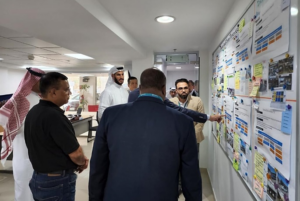
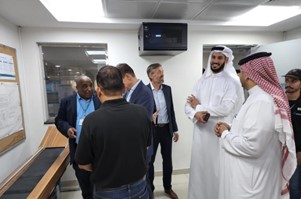
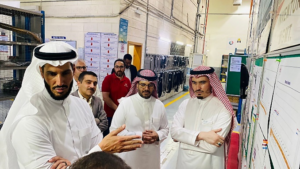
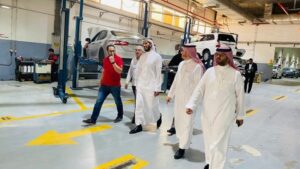
Comment l’initiative a-t-elle été reçue au sein d’Abdul Latif Jameel ?
De manière très positive. Pas seulement par la direction, mais plus important encore pour moi, par les personnes qui comptent vraiment : les personnes de première ligne, celles qui sont quotidiennement en charge de répondre aux besoins de nos clients.
Lorsque je me rends dans un endroit qui n’a encore jamais été « le meilleur de la ville », des personnes me demandent quand cela arrivera, parce qu’elles ont entendu des choses très positives à ce sujet.
À l’avenir, comment cet état d’esprit d’amélioration continue peut-il aider Abdul Latif Jameel dans sa réussite continue ?
Notre objectif en tant qu’entreprise est de nous assurer que notre culture est une culture qui croit et agit sur l’amélioration continue de façon perpétuelle.
C’est très difficile à atteindre, mais si nous pouvons construire, au sein d’Abdul Latif Jameel, une culture où l’amélioration continue est l’état d’esprit par défaut, une approche automatique que tout le monde suit sans même y penser, menée par une génération de leaders avec cette façon de penser, ce serait une avancée très puissante.
Nous n’y sommes pas encore, mais c’est ce que nous nous efforçons de faire.
Plus jeune, vous êtes allé à Toyota au Japon et vous avez été immergé dans la culture Kaizen. Comment cela a-t-il changé votre façon de voir la vie ?
De manière fondamentale. Kaizen est une façon si simple de voir la vie. C’est pour cela que ça m’a touché à ce point. J’essaie de garder les choses aussi simples qu’elles peuvent l’être, car une fois que vous les compliquez, les solutions deviennent également plus compliquées. Cela commence par de petites choses, comme faire votre lit tous les matins. Si vous le faites, vous commencez la journée par un premier petit succès.
Cela m’a également appris qu’il faut toujours s’efforcer de s’améliorer, et de rester humble à ce sujet.
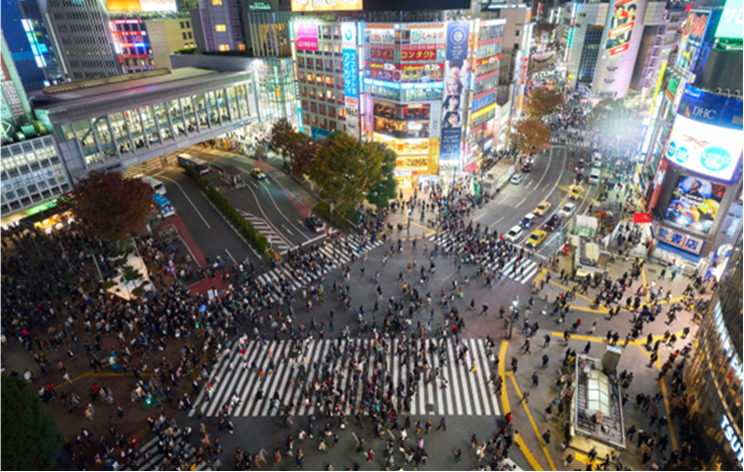
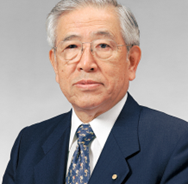
Je me souviens que mon père a diné une fois avec le Dr Shoichiro Toyoda, fondateur de Toyota.
Ils parlaient de la « Toyota Way » et mon père lui a demandé : « Qu’est-ce que cela signifie pour vous ? »
Le Dr Toyota a répondu : « J’apprends toujours ! »
Plus tard, j’ai réfléchi à ce qu’il avait voulu dire, et cela m’a vraiment frappé. Ce que cela signifie, c’est l’humilité…
Être conscient et suffisamment humble pour comprendre que tout le monde peut toujours apprendre et s’améliorer ; cela signifie comprendre en profondeur, et donc avancer continuellement, ce qui est l’essence même du Kaizen.
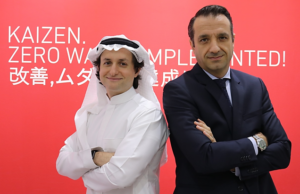
En fait, l’engagement d’Abdul Latif Jameel en faveur de l’amélioration continue est tel qu’en 2017, nous avons formé une co-entreprise avec le cabinet de conseil « Lean Management », Four Principles, pour diffuser les idées dans la région du Moyen-Orient et au-delà. Le but est d’aider les organisations du secteur privé et public à tirer parti des opportunités qu’il peut offrir.