Shuqaiq 3: pushing the boundaries of innovation
The Shuqaiq 3 desalination plant in Jizan province in south-west Saudi Arabia will be one of the largest Reverse Osmosis (RO) desalination plants in the world when complete in the fourth quarter of 2021.
Awarded to a consortium of Almar Water Solutions (through Abdul Latif Jameel Enterprises), Acciona, Marubeni Corporation and Rawafid Alhadarah Holding Co, its 450,000 cubic meter daily production capacity from this US$ 600m infrastructure investment will guarantee the supply of drinking water to over 1.8 million citizens, while also contributing to economic and industrial development both locally and nationally.
Recognized throughout the water industry as one of the most complex and innovative plants of its kind, in September 2019 it was named the ‘Utilities Project of the Year’ at the Middle East Energy Awards 2019, held in Dubai, UAE, cementing its status as one of the flagship new infrastructure projects in the region. Despite COVID-19, the project has managed to stay on track, with procurement and engineering kept on time and a very impressive – and ongoing – site safety record.
As part of a series of interviews with people involved in the project, Luis Morales, Technical Director at Shuqaiq 3, discusses the complexities of the development and how the team has successfully kept the project on track despite unprecedented global disruption.
How has progress been so far and what have been the biggest technical challenges you’ve had to address?
Technically speaking, the biggest challenge was minimizing the electrical consumption and optimizing the energy efficiency of the plant, not only for the construction and operation, but for the tender to be competitive enough to be awarded the project in the first place. We’ve worked closely with vendors and suppliers to find the best equipment with the lowest energy consumption, as well as with the engineers to implement a design which could optimize the process. It was the only way we could build a strong enough competitive position to win the tender. Now we have a plant which is highly optimized and respects the environment, which is extremely important to us.
How was the progress of the project effect by the COVID-19 pandemic?
It won’t surprise you to know that the pandemic had a big impact on our progress. We faced a lot of potential delays. To avoid these delays, we were very proactive, and we worked with our contractors to develop different solutions. For example, we changed the process for installing the intake. We had originally planned to construct the intake from the sea to the shore. But we switched it around and built it from the shore to the sea instead, which meant we could start taking in water even before finalizing the works. To do that, we had to change a lot of processes, such as providing new launch areas where the welding team could work on the pipes, and that was very challenging.
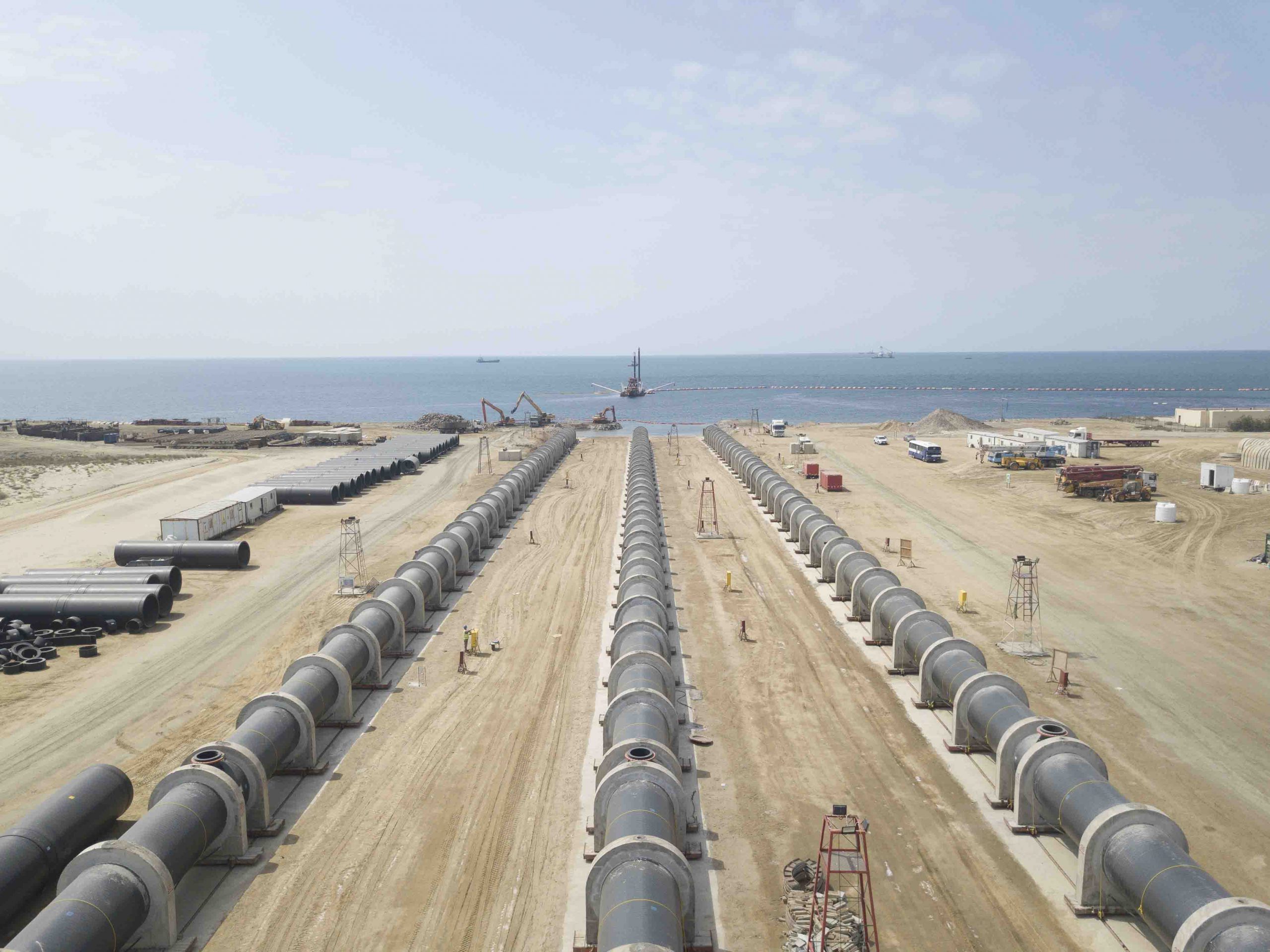
You mentioned the importance of making this plant as energy efficient as possible. How did you achieve this?
Energy efficiency was essential to our bid. To achieve it, it’s not enough to simply ask a supplier for a more efficient pump or a better motor. We had to be a lot more innovative in terms of the processes themselves. We adapted our designs to reduce energy consumption. We worked with membrane suppliers to adapt the membranes so they would function more efficiently in deep seawater, for example. We designed a system that uses high pressure pumps installed in a ‘frame’, rather than individually. This allows us to manage all the pumps at the same time, which significantly improves efficiency. We use a two-pass process for the water, whereby it passes through the membranes twice. By carefully analyzing the data, we can tweak this process to find the perfect distribution between the first and the second pass to improve efficiency even more.
In addition, we worked with our technical specialists to reduce the water pump pressure from 4.5 bars to 3.9. This may not seem like a lot, but in terms of the amount of water we produce – 450,000 cubic meters – this small reduction in pressure results in very big gains in energy efficiency.
Does Almar Water Solutions have strong expertise and experience to enable it to innovate in this way?
Yes, we’ve previously worked on projects all over the world and we’ve been able to use the experience and knowledge we’ve gained to benefit Shuqaiq 3. Also, the strong relationships we have built up over the years with vendors and suppliers helps us keep on top of the latest innovations and techniques.
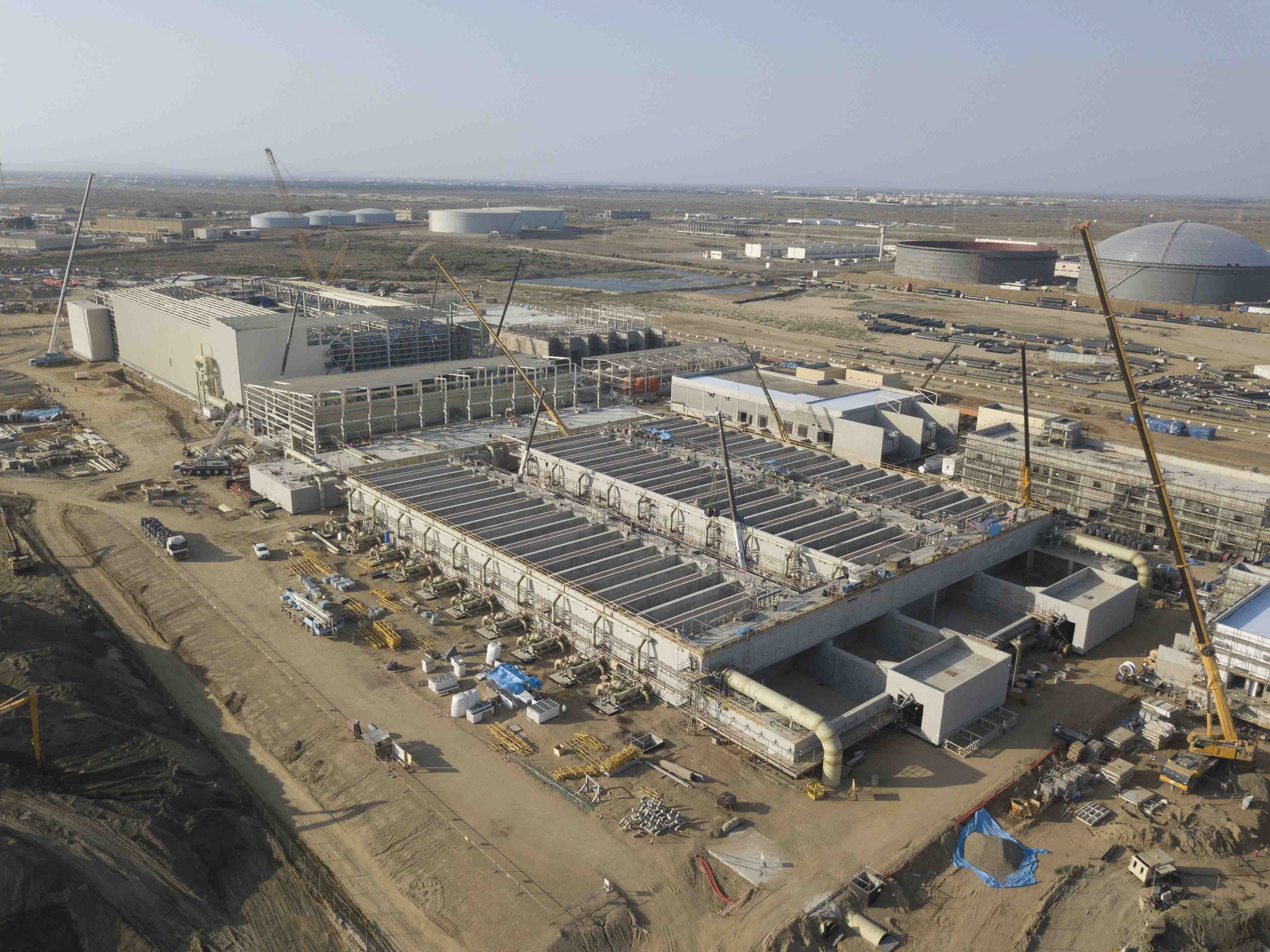
Shuqaiq 3 uses Reverse Osmosis technology to produce desalinated water. Were other technologies considered?
In this case, the tender documents specified reverse osmosis, so we did not have any say in which technology was used. But even if we did, we would have chosen Reverse Osmosis because it’s the most efficient and the best technology currently available for desalinating seawater.
There are other technologies, but they tend be older and less efficient, whereas Reverse Osmosis is getting more efficient and more competitive all the time. There is a lot of investment into new materials, new solutions and techniques for improving the efficiency even further. It’s quite exciting to see how the technology develops over the next few years.
There are already two other water plants in that location, Shuqaiq 1 and Shuqaiq 2. The new plant sits between them. Did this present any additional challenges?
Yes, it did, principally one of space. On shore, we have plenty of space, but offshore, the amount of space is more restricted. The intakes from the other two plants lie on both sides of our plant, so we had to be very careful during the marine works. That was probably the most technically challenging aspect of the construction, not only because it is 1.5km of pipe installation, but also because we have to be sure that we are not impacting the intakes of Shuqaiq 1 and 2 during our marine works. We put in place strict control measures to avoid increasing turbidity in the water, for example. Shuqaiq 2 also produces power as well as water, so there are quite a lot of ship movements in and out, bringing in fuel, oil and so forth, which also created additional challenges. We have a good relationship with both our neighbors, so it wasn’t a problem, but we had to be very careful at all times.
The plant is on the shores of the Red Sea. What is the water like in that area?
The water in the Red Sea is beautiful, but it is warm and very rich in organisms. It is fantastic in terms of biodiversity but makes the desalination process more difficult. We are working with an average water temperature of around 30 degrees and the high level of biological growth is dangerous for the process. We have to constantly monitor and control this risk. On the other hand, the turbidity is good, which is an advantage. However, we knew this from the outset and, thanks to our strong relationships with the other plants nearby, we have been able to learn from their experiences to implement effective solutions to these problems. For example, to minimize biological growth (biofouling with algae, etc.) we are implementing a so-called ‘pigging system’. This is where we use pressurized water to fire a plastic ‘bullet’ along the pipes to clean the biological growth off the inside, so we can maintain a consistent volume of water in the intake. We have also been working with the membrane supplier to ensure we can maintain productivity at this water temperature and avoid any potential risk of damaging the membranes.
Membranes are a crucial part of the desalination process. How many membranes do you use?
Our process uses around 54,000 membranes in two passes: 41,000 in the first and 13,000 in the second. Each membrane is around 1m in length, so we are talking about 54km of membranes in total.
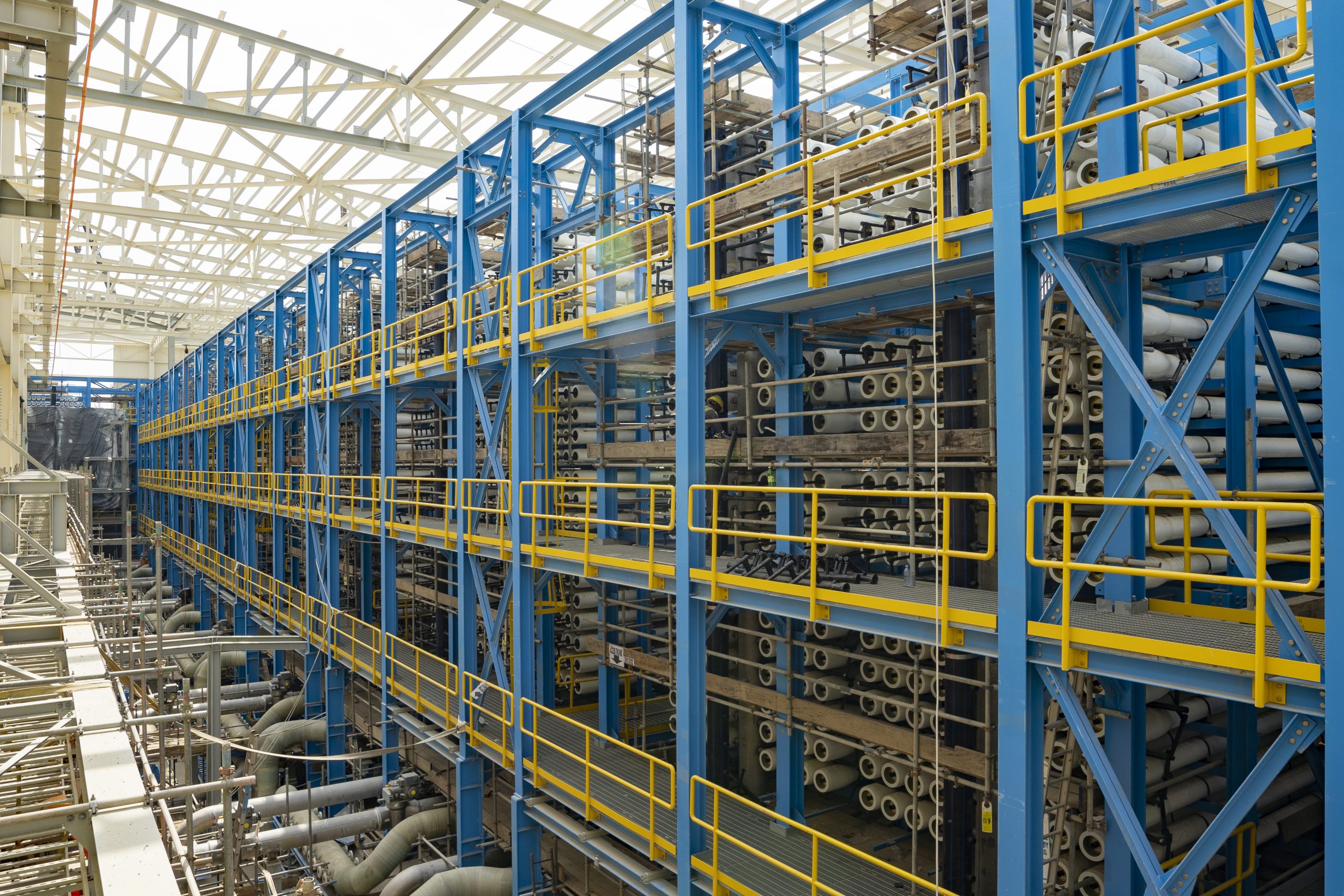
How does the productivity of Shuqaiq 3 compare to previous generations of desalination plants?
In the 2000s, plants usually produced between 50,000 cubic meters and 100,000 cubic meters. By the 2010s, this had increased to around 200,000, with the biggest one in the world achieving 400,000 cubic meters. Shuqaiq 3 is 450,000 cubic meters – so even bigger than the then biggest to date and still probably in the world top 10 of commissioned plants.
They are building some other huge plants in Saudi Arabia, but even when they are completed, Shuqaiq 3 will still be in the top 5 biggest plants in terms of production capacity.
Almar Water Solutions is part of a consortium of partners developing Shuqaiq 3. How important is a partnership approach in a project like this?
I think it is essential. In our consortium, Almar has the technical knowledge, expertise and previous experience of this kind of development. But a project like this is about much more than construction.
It needs finance expertise, project management, investment, operations, and so on. Working with other partners means the consortium benefits from bringing in all these other complementary areas of expertise. And our partnership has worked well. We have built strong relationships within the consortium, and this has benefitted the project enormously.
Environmental issues have become much more important in recent years. What measures are being taken to minimize the environmental impact of Shuqaiq 3?
Optimizing the sustainability of the plant is something that fully aligns with own values and way of doing business at Almar Water Solutions. We want to respect the environment at every stage, not only during construction, but also during operation. We have implemented a number of measures and technologies to help us achieve this. For example, this plant has a sludge treatment facility to treat all the material we remove from the seawater during desalination. Not all desalination plants have a facility like this. It means that all the waste we produce is innocuous and not harmful to the environment.
The pigging system we use to clean the inside of the pipes is also environmentally friendly. It is a mechanical cleaning system, which means we can avoid using chemicals to clean out the intake pipes and intake tower, so we can limit the amount of hypochlorite we use.
Finally, during the construction phase, we are using strategies that are more respectful to the marine environment. For example, when we buried the pipes in the sea floor, we removed a lot of mud. But instead of just dumping this mud somewhere else and disrupting the marine environment, we used sucker dredgers to take this material out of the sea. We store it. We dry it, and then we use it to backfill the pipe trenches – so essentially, we are putting it back in the location it came from. Similarly, with the brine from the desalinated water, we disperse it back into the sea at various points along a 200 meter pipe, so it disperses very quickly in the ocean and does not overload one particular area.
You have worked on previous Almar projects. How does this one compare to others you have worked on?
I’ve worked on previous Almar projects in other locations, and also for other projects around the world in my previous lives. Each one is very different, depending on the local circumstances. Shuqaiq 3 is probably the most memorable because it had the added complication of the COVID-19 situation, particularly from March to September 2020. There were curfews, delays in supplies, people couldn’t travel. It was a very difficult at time, but I’m very proud that we made it through successfully and kept the project moving forward to meet its key dates. The main key date now is the commissioning date at the end of October 2021, but I’m confident we will achieve it.